【湖北大力 原创】前段时间湖北大力报道过一个奥铃传动轴脱落的事故,引起了不少人的关注,那辆车是由于传动轴螺丝脱落导致传动轴晃动并最后出现脱落。在分析事故原因的过程中,我们也注意到各个厂家在传动轴支撑角板的设计强度也不一样,这其实也存在一定的安全隐患。
目前中轻型卡车的设计偏向于长轴距与高承载性,当驱动桥与变速器之间的距离不大时(短轴距),普遍采用两个万向节与一根传动轴的传动结构。当驱动桥与变速器相距较远(长轴距),传动轴长度超过1.5米时,自振频率低,容易出现共振。为了提高传动轴的临界转速,常将传动轴断开两根或三根,万向节三个或四个。这个时候,必须在中间传动轴上加设中间支撑。
● 传动轴支撑角板的由来
万向节所连两轴之间的夹角,理论设计要求不超过15°- 20°,即使4X4越野汽车(特别是短轴距),最大也不超过30°。传动轴夹角的大小直接影响到万向节十字轴和滚针轴承的寿命,万向节传动的效率和十字轴旋转的不均匀性。
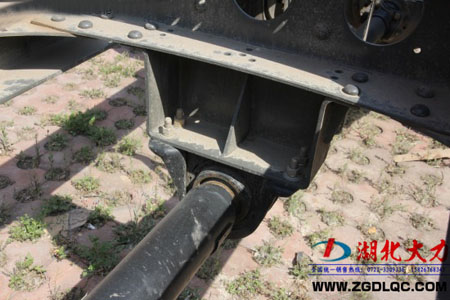
上图即为传动轴中间支承的附加角板,减小了万向节的夹角,这一布置形式已为我们所常见。
● 传动轴中间支撑的常见形式
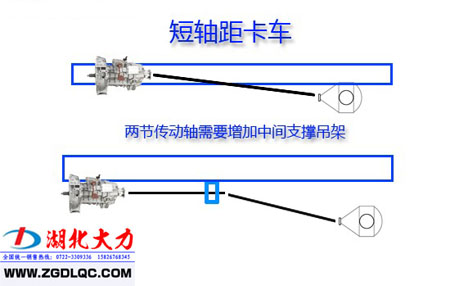
短、长轴距不同的传动轴布置形式
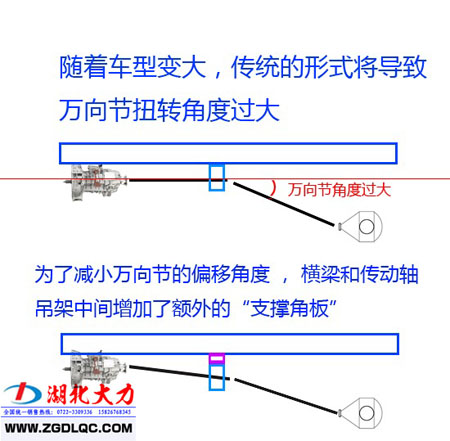
底盘高度决定传动轴夹角的变化
● 传动轴中间支撑的振动特性与故障延伸性
传动轴中间支撑出现故障的原因很多,最常见的故障我们称之“吊架皮圈”损坏,也就是传动轴中间支撑其中橡胶减震元件的损坏。如果出现传动轴弯曲、动平衡失效、十字轴松旷,传动轴中间支撑将承受严重振动负荷,损坏也就不可避免。
支撑角板的损坏也时有发生,甚至中间支撑并没有损坏而角板首先变形报废,这又是何原因呢?
典型案例:
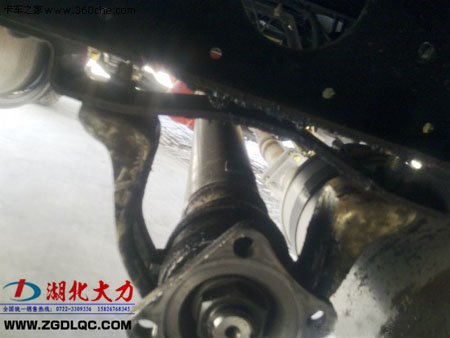
传动轴中间支承角板严重变形
上图这类车型的支撑角板设计并非刚性连接,这辆车因传动轴螺栓松动,造成了严重故障。分析其原因,当传动轴径向全跳动大于0.5mm-0.8mm时,振动力量和频率随传动轴的转速变化加重。一旦传动轴螺栓折断,传动轴中间支撑中橡胶缓冲元件与角板的下端面,同时发生严重变形和损坏。
● 同吨位级别中间支承角板设计对比图与说明
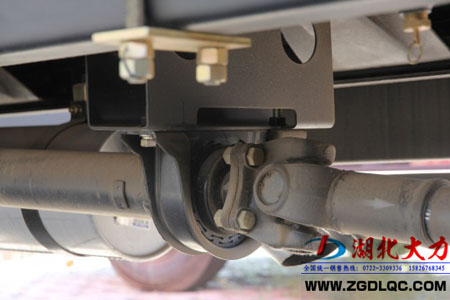
刚性传动轴支撑角板(欧马可)
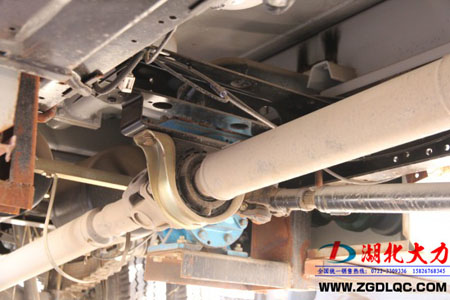
柔性传动轴支撑角板(奥铃)
通过上面两张图篇的对比我们看到,不同两款卡车虽然是同吨位级别的,但传动轴中间支撑角板的设计思路完全不同。一款采用刚性设计,加固了角板的受力点的强度。另一款轻卡车型考虑欠缺,柔性连接的设计在同系列卡车中显得过于单薄。
● 常见故障的原因与解决办法
传动轴中间支撑是很关键的部件,损坏之后如果造成传动轴脱落是严重的事故隐患,行车安全将受到极大威胁。
为了避免造成更大的损失,我们可以更换刚性连接的支承角板,也可以自己动手加固原有的支撑角板总成。除此之外,经常仔细检查传动轴各部件也是非常重要的,传动轴螺栓需要选择高强度自锁式配套产品。如果传动轴有异响,要重点检查传动轴锁紧螺母。
Tag: